Table of Contents
Table of Contents
Introduction and Basic Principles
From the preceding three articles on evaluating an engine’s power potential it should be clear that you can never have too much inlet valve area. It directly determines power potential – every 10% increase in inlet valve area gives a 10% increase in power potential. However, in many engines there is a trade-off between inlet and exhaust valve size. By making one smaller you can increase the size of the other. Equally this is not always the case. Sometimes a larger inlet valve will hit the bore wall long before it interferes with the exhaust valve or vice versa.
On engines with angled valves, i.e. angled towards each other, the point of interference depends on the cam duration as well as the absolute valve size. Long duration cams with a lot of overlap will have both valves open a long way at TDC on the exhaust stroke which is where they can hit each other. With shorter duration cams you can make either valve bigger and still not have clearance problems. Clearly all engines need exhaust valves and if these are too small power will suffer. So when the choice is between increasing inlet valve size and exhaust valve size what do you do?
The Relationship Between Exhaust Valve Size and Power
The simple answer is there are no simple answers because optimum exhaust valve size, or more correctly optimum ratio of inlet to exhaust valve size, depends on a number of factors including the state of tune of the engine, cylinder head design, port efficiency, cam profile and especially compression ratio. However there are some very good rules of thumb which will put you very close to optimum for most normal tuned engines.
The first thing to appreciate is that exhaust valve area does not directly relate to power potential. As an approximation for an average engine if you increase exhaust valve area by 10% you only add about 1% to 2% to the engine’s power potential. This is a very much less direct relationship than that between inlet valve area and power. What happens when the exhaust valve is too small is you generate a pumping loss where the piston has to do the work of forcing out the last of the exhaust gasses but this is a small penalty compared with the direct loss of losing inlet valve flow because the inlet valves are smaller than they otherwise could be.
Only when the exhaust valves are very much too small do the power losses start to become significant. What also follows from this is that you have to be talking about very highly developed engines where the last couple of bhp is important before you have to worry too much about whether it’s better to make the inlet valve 0.5mm bigger at the expense of a 0.5mm smaller exhaust valve or vice-versa. For most engines fitting bigger exhaust valves will make an absolutely negligible difference to the engine’s power output and in many cases they will already be too large.
Forced Induction Engines and Exhaust Valve Requirements
The other commonly quoted situation is that of turbocharged and supercharged engines. Ask most people, many “professional” engine builders included I’m afraid, and they’ll tell you forced induction engines need bigger exhaust valves at the expense of smaller inlet ones. Well after all it stands to sense dunnit mate? The inlet side has a thumping great turbo pushing the air in and the exhaust side has nothing extra to help it. Utter bollocks I’m afraid and anyone who tells you this can be discounted as any sort of authority on how engines work and probably best avoided if you’re looking for someone to spend your money with.
When you turbocharger an engine you increase the cylinder pressure in direct proportion to the boost because you’ve crammed more air into it. This extra cylinder pressure directly increases the exhaust valve flow when the exhaust valve opens. In effect everything stays in the same proportion as when the engine was normally aspirated. The turbo basically boosts the exhaust valve flow in exactly the same proportion as it boosts the inlet valve flow although the relationship, being one step removed, is too remote for most people to appreciate it. So forced induction engines actually follow exactly the same rules about exhaust valve size as normally aspirated ones.
Problems with Oversized Exhaust Valves
Can the exhaust valve be too big? Indeed it can unless certain steps are taken to design other aspects of the engine to suit the valve size. The main adverse effect of large exhaust valves is in the overlap period at the end of the exhaust stroke when the exhaust valve is closing and the inlet one opening. While both valves are open at the same time some rather nasty things can happen.
Fresh inlet charge can skip straight across to the open exhaust valve and disappear down the exhaust port leading to high hydrocarbon emissions and poor cylinder filling. Also the exhaust gasses can reverse flow at low engine speed and come back up the exhaust pipe and into the cylinder leading to contamination of the fresh inlet charge. To combat these effects you can reduce cam duration but this then adversely affects high rpm power. Alternatively you can increase the cam lobe centreline angle (LCA) so the exhaust cam closes earlier and the inlet one opens later.
This reduces the ‘valve overlap triangle’ but again might not be what you want at higher rpm. What we can deduce from this is that large exhaust valves might have little adverse effect on low tuned or standard road engines with short duration cams but progressively worse effects on higher tuned engines with long duration cams. In fact it leads us to the inevitable, and somewhat extraordinary, conclusion that the higher we tune an engine the smaller the exhaust valve might need to be. This flies in the face of everything most people believe about tuning where bigger is always better in respect of just about every component.
Determining Optimal Exhaust Valve Size
So let’s get down to some rules. How do we decide if the exhaust valve is too small or too big? One way is to set a ratio between inlet valve size and exhaust valve size. Unfortunately this ratio changes as the state of tune of the engine changes so we need to specify the state of tune of the engine.
Exhaust to Inlet Valve Ratios by Engine Type
State of Tune | Exhaust/Inlet valve ratio by diameter | Exhaust/Inlet valve ratio by area |
---|---|---|
Low tuned engines, historic engines, forced induction engines, CR less than 9:1 | 87% to 89% | 75% to 80% |
Normally aspirated fast road/mild rally engines, short/medium duration cams, CR 9 to 10.5 | 84% to 87% | 70% to 75% |
Highly tuned engines, longer duration cams, rally or race spec, CR 10.5 to 13 | 81% to 84% | 65% to 70% |
Very high CR engines perhaps with artificial induction system restrictions, CR 13 to 16 | 77% to 81% | 60% to 65% |
An example of the type of engine referred to in the last row above would be race engines where the induction system has to breath through a restrictor to limit power and so the compression ratio is raised to unusually high levels to squeeze as much as possible from the incoming charge. An engine without such induction restriction would detonate at CR levels like this. This category can also include engines with limited inlet flow capability simply because of design i.e. older style 2v per cylinder engines like the Chevy V8.
Exhaust Valve Size by Cylinder Displacement
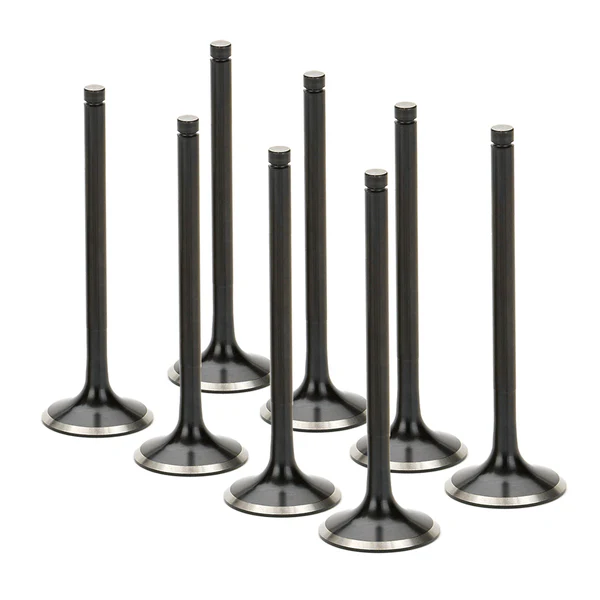
If the exhaust valves in your engine are at least this big then you’ll see very little if any benefit from making them bigger even if you tune the engine for fast road, rally or race use and fit bigger inlet valves. The proviso is that you modify the exhaust ports properly to make the exhaust valves flow well but that’s another subject. There’s no point in having big enough exhaust valves if the port is restrictive or you don’t know how to modify it properly.
Another way is to gauge the exhaust valve size in relation to the cylinder size. If we tune the engine by fitting larger inlet valves, longer duration cams and raising the CR the exhaust/inlet valve size ratio decreases but then we usually want that to happen anyway as explained above so in fact everything stays correct in relation to the state of tune of the engine. What I set out below is a table which shows a sensible exhaust valve size for a given cylinder size for average car engines. This table isn’t going to apply to engines with abnormally large bore/stroke ratios such as motorbike engines or custom designed formula race series engines where you’ll have to go back to the ratios in the table above.
Cylinder Size cc | Exhaust Valve Size 2v per cylinder engine | Exhaust Valve Size 4v per cylinder engine |
---|---|---|
300 | 30mm | 23.5mm |
350 | 32mm | 24.75mm |
400 | 33.5mm | 26mm |
450 | 34.75mm | 27mm |
500 | 36mm | 28mm |
550 | 37.5mm | 29mm |
600 | 38.25mm | 30mm |
650 | 40mm | 31mm |
700 | 41.5mm | 32mm |
Given that it costs the same or more to fit bigger exhaust valves as inlet ones then it’s clearly a sensible idea to spend the money on the inlet side of the engine. Of course if you’re trying to build something world beating then no doubt you have the budget to dyno test all possible combinations of valve size and you might well deviate from the table.
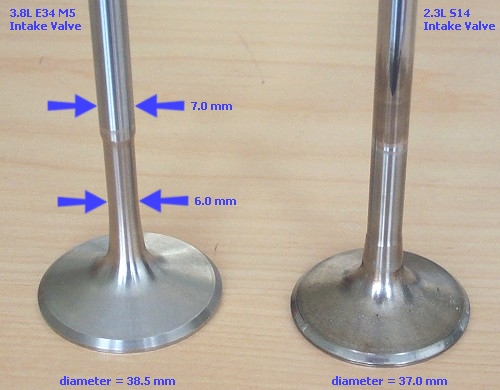