Table of Contents
Table of Contents
The Effects of Lightening a Flywheel on Vehicle Performance
When the flywheel of a car is lightened it can have a great effect on acceleration – much more than just the weight saving as a proportion of the total vehicle weight would account for. This is because rotating components store rotational energy as well as having to be accelerated in a linear direction along with the rest of the car’s mass. The faster a component rotates, the greater the amount of rotational kinetic energy that ends up being stored in it.
The Physics Behind the Effect Lightening Flywheels
The engine turns potential energy from fuel into kinetic energy of motion when it accelerates a vehicle. Any energy that ends up being stored in rotating components is not available to accelerate the car in a linear direction – so reducing the mass (or more properly the “moment of inertia”) of these components leaves more of the engine’s output to accelerate the car. It can be useful to know how much weight we would need to remove from the chassis to equate to removing a given amount of weight from the flywheel (or any other rotating component).
Mathematical Analysis
There is more than one way of solving this equation – we can work out the torque and forces acting on the various components and hence calculate the accelerations involved – also we can solve it by considering the kinetic energy of the system. The latter approach is simpler to explain so this is the one shown below.
Let’s imagine we take two identical cars – to car A we add 1 Kg of mass to the circumference of the flywheel at radius “r” from the centre. To car B we add exactly the right amount of mass to the chassis so that both cars continue to accelerate at the same rate. If we accelerate both cars for the same amount of time they will end up at the same speed and will have absorbed the same amount of kinetic energy from the engine. In other words, the additional 1 Kg in the flywheel of car A will have stored the same amount of kinetic energy as the additional M Kg of mass in the chassis of car B. To solve the problem of the size of M we need to use the following definitions:
V – the speed of either car after the period of acceleration R – the tyre radius G – the total gearing (i.e. the number of engine revolutions for each tyre revolution) r – the flywheel radius (i.e. the radius at which the extra mass has been added to car A) M – the amount of mass added to the chassis of car B
Kinetic energy is proportional to ½mv² – the kinetic energy stored in the extra chassis mass in car B is therefore ½MV².
The extra 1 Kg of flywheel mass in car A stores linear kinetic energy in the same way as if it were just part of the chassis. After all, every part of the car is travelling at V m/s – so it stores linear kinetic energy of ½ x 1 x V² = ½V².
To find out how much rotational kinetic energy the 1 Kg stores, we need to know the speed the flywheel circumference is travelling at. The car is travelling at the same speed as the circumference of the tyre (assuming no tyre slip of course). We know that for every revolution of the tyre, the flywheel makes G revolutions. However the flywheel is a different size to the tyre – so the speed of the circumference of the flywheel is VGr/R. The rotational kinetic energy is therefore ½(VGr/R)².
Now we can put the whole equation together – the extra kinetic energy in the chassis of car B = the sum of the linear and rotational kinetic energies in the 1 Kg of flywheel mass of car A – therefore: ½MV² = ½V² + ½(VGr/R)² => ½MV² = ½V² + ½V²(Gr/R)² => divide both sides by ½V² to arrive at the final equation: M = 1 + (Gr/R)²
That wasn’t so bad then – we managed to avoid using true rotational dynamics involving radians and moments of inertia by considering the actual speed of the flywheel circumference. This did of course involve assuming that all the mass added or removed from the flywheel was at the same radius from the centre. In the real world that is not going to be the case so we need to use moments of inertia rather than mass to solve the equation. The simple equation above is useful though in getting an idea of the relative effect of lightening components provided we have a good idea of the average radius that the metal is removed from.
Practical Implications
It can be seen that gearing is an important factor in this equation. The higher the gearing the greater the effect of reducing weight – so for a real car the effect is large in 1st gear and progressively less important in the higher gears. We can also hopefully see that when r is larger, so is the effective chassis weight M. So removing mass from the outside of the flywheel is more effective than removing it from nearer the centre.
It might at first look as though tyre diameter is important but of course it isn’t for a real car – if tyre size was to change then so would gearing have to if overall mph per thousand rpm were to stay the same – the two factors would then cancel out again.
To show the sort of numbers that a real car might have, I did some calculations based on a car with average gear ratios and tyre sizes – the table below shows the number of Kg of mass that would have to be removed from the chassis to equate to 1 Kg removed from the O/D of the flywheel at a radius of 5 inches.
GEAR MASS KG 1 39 2 12 3 6 4 4 5 3
So in first and second gear this is a pretty important effect – I built an engine recently and managed to remove nearly 3 Kg from the outside of the standard flywheel – so that would be equivalent to lightening the car by over 100 Kg in 1st gear – not to be sneezed at in terms of acceleration from rest. With special steel or aluminium flywheels even more “moment of inertia” can be saved. The recent trend in racing engines to using very small and light paddle clutches and flywheels is therefore more effective in terms of the overall performance of the vehicle than it might first appear.
Special Considerations for Different Engine Types
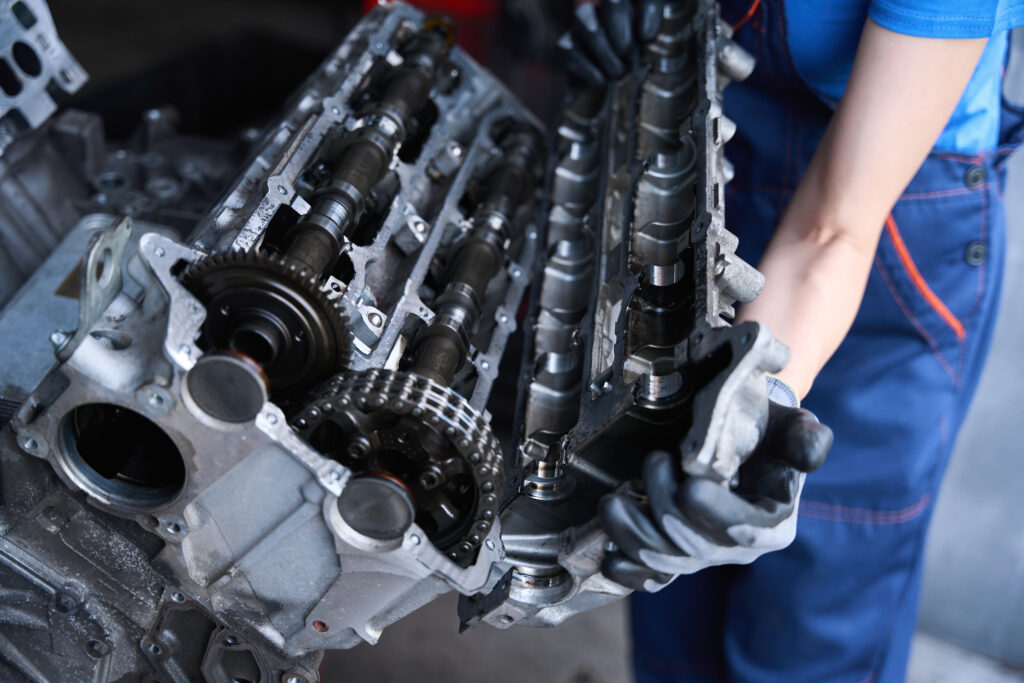
There’s a final consequence of the “flywheel effect” being dependent on gearing. Small highly tuned, high revving engines need to run much higher (numerically) gearing than large, low tuned engines. This means that the effect can be very pronounced on them. Bike engines are a good case in point, especially as they are now starting to be used in cars so much. A 100 bhp bike engine might only be 600cc and rev to 12,000 rpm. A 100 bhp car engine might be 2 litres and rev to 5,500 rpm.
Put the bike engine in a car and you’ll need to run a final drive ratio twice as high as for the car engine. As the flywheel effect is proportional to the square of gearing, it will be 4 times as high for the bike engine. You could therefore be talking about 1kg off the flywheel being equivalent to 160kg off the weight of the car. That’s why bike engines have such small multiplane clutches to keep the moment of inertia down. On the other side of the coin, it’s not worth spending much money lightening the flywheel of a 7 litre Chevy engine revving to under 5,000 and geared for 60 mph in first as the vehicle will be very insensitive to the reduction in weight.
Safety Considerations
If you are going to get your standard cast iron road car flywheel lightened then be sure to take it to a proper vehicle engineer and not just your local machine shop. Take off too much material and it might be weakened so much that it explodes in use. Given that flywheels (at least in rear wheel drive cars) tend to be situated about level with your feet, it isn’t worth the extra acceleration if you lose both feet when the ring gear comes out through the side of the transmission tunnel like a buzz saw at 7,000 rpm.
There are plenty of ex racing drivers hobbling about on crutches who’ll tell you that this can and does happen. On FWD cars the effects can even more unpleasant – a flywheel entering the cabin can give you a split personality starting from just below the waist that will put quite a crimp in your day. Also when you remove any weight from the flywheel it will need re-balancing again properly. We’ll be happy to do the job for you if you don’t know of an experienced engineering shop.
A Cautionary Tale

A friend, told me an interesting story the other day which relates to my warning above about lightening flywheels properly. He was at the local engine reconditioner chatting to the proprietor about having a cylinder head skimmed. At the back of the workshop, one of the lads who worked there was lightening a flywheel on the lathe. Suddenly there was an almighty bang and a lot of swearing so Garry and the owner went back to see what had happened.
The lad had been removing material from the centre of the flywheel, just outboard of where the 6 crankshaft bolt holes are. For starters this is a stupid place to remove material because it is a highly stressed area and also much less effective in terms of the reduction in inertia than removing material from the rim of the flywheel. Anyway, to cut a long story short this idiot had machined right through the flywheel leaving the centre attached to the chuck of the lathe and the rest had flown off and bounced across the workshop.
It made me wonder what would have happened if he’d stopped just short of machining right through, say with only 1mm thickness of material left, without realising how thin and weak he’d made it. It would then have failed in the car, maybe at high rpm, and done the sort of damage I describe above. The moral is clear. Get critical work like this done by someone who knows what they are doing.
An average cost to lighten and rebalance a cast iron flywheel it £80 but best to email and ask about your specific application first.
Other Rotating Components
All other components which rotate absorb energy in addition to them having to be accelerated linearly along with the chassis. Components which rotate at engine speed like flywheels are the most cost effective ones to lighten in terms of their equivalent chassis mass but it pays not to overlook the mass of any rotating component. The next major category is items which rotate at wheel speed – wheels, tyres, discs etc. These don’t rotate as fast as engine components but they can be very heavy.
The average car wheel and tyre weigh about 45 lbs together. A good rule of thumb is that in addition to its own normal weight a wheel speed item adds the equivalent of an extra 3/4 of its mass to the effective chassis mass and this figure is not dependent on gearing so it stays a constant at all times. It’s a smaller effect than the flywheel effect which can be many times its own mass in first gear but still important. Let’s say you fit wide wheels and tyres to your car.
If each corner weighs an extra 10 lbs more than the standard items then the effective increase in chassis mass is 40 lbs for the direct weight plus another 30 lbs being 3/4 of the direct mass – a total of 70 lbs. On a light car like a Westfield or hill climb single seater this could be between 5% and 7% of the effective total car weight. Equivalent to knocking the same percentage off the engine’s power in acceleration terms. That’s why F1 and other high tech series designers strive so hard to reduce weight in this area and use magnesium instead of aluminium for wheels and the thinnest possible carcasses for tyres.
It also reduces unsprang weight of course which helps the suspension and handling. Even on a 1 ton road car the effect of heavy wheels and tyres can be noticeable in terms of reduced acceleration. Wider tyres also absorb a bit more power in friction which doesn’t help either if the engine is on the small side.
The other few rotating items, gearbox internals, camshafts etc are generally of small diameter and not worth lightening because of their consequent low inertia. One thing I can promise you is that the current fad for anodised aluminium cam pulleys which then usually get hidden behind a cover anyway won’t make a scrap of difference to your engine because of the few grams weight they save. They may well wear out and cost you your entire engine if the teeth strip off the belt though. Aluminium is not really the material for gears and sprockets but when did fashion and common sense ever go together?
Common Misconceptions
Finally, you see some frankly unbelievable comments on car forums about lightened flywheels such as “they might make the car faster on the flat but it’ll be slower up hills because that’s where inertia helps you.” Yeah right, heavy things go up hills so much better than light ones. That must be why all those trucks I overtake on the motorway come flying back past me up the next rise and then I overtake them again on the way down. A lightened flywheel has exactly the same effect as making the car lighter – no more no less. It will make the car faster everywhere – up hills, down hills, round my lady’s chamber.
Also lightening the flywheel does NOT give the engine any more horsepower just like removing a sack of cement from the boot doesn’t either. It simply leaves more of the horsepower available to accelerate the car because less is wasted in accelerating the flywheel.
Potential Downsides and Benefits
Is there a downside? The only one of note is the idle quality. To get really smooth low rpm idle you need some flywheel mass to smooth the power pulses as each piston goes over TDC. This is more important the fewer cylinders the engine has. However in my experience it’s simply not possible to lighten a standard cast iron flywheel so much that it greatly affects the idle quality. In fact some standard cars like Peugeots manage with very light flywheels anyway whereas others use a lot more mass most of which is unnecessary. For a track car none of this is even an issue though.
Any other upsides? One thing you’ll find is the car will slow down much faster under engine braking because it doesn’t have the flywheel inertia dragging it on. I much prefer a road car to be like this and you’ll find you need to use the brakes less in normal driving.