Table of Contents
Table of Contents
Understanding Turbo Engine Fundamentals
There are some very common misconceptions out there about tuning turbo engines. In particular whether improving flow through cylinder head and induction system porting makes any difference to power or whether all you have to do is turn the boost up. The simple answer is that improving flow can be even more important on a turbo engine than a normally aspirated (N/A) one. All engines make power in proportion to the amount of air they can breathe and anything that increases air flow into the cylinders increases power.
A N/A engine relies solely on the 14.7 psi of atmospheric pressure to push air into the cylinders when the valves open. With no way of increasing this pressure it’s pretty well understood by most people that you have to improve the flow ability of the head and induction system to get more air through in a given time. So why the confusion about turbos? In fact a turbo engine is really only a N/A engine operating at a higher than standard inlet manifold pressure.
If this were a larger planet with a thicker atmosphere it might well be that standard atmospheric pressure could be 30 psi instead of 14.7 psi. Engines would then produce twice the horsepower from the same capacity but tuning mods would still concentrate on improving induction system flow in exactly the same way as they do at 14.7 psi. Fitting a turbo to boost inlet manifold pressure from 14.7 psi to 30 psi just makes an engine on this planet run in a similar way to a N/A one on a bigger planet and the same mods will improve power on both.
The Physics of Boost and Flow Restriction
To generate a pressure difference there has to be a resistance to flow. Try blowing as hard as you can through a straw and then do the same just through your open mouth. You can generate enough pressure through the straw to puff your cheeks out and almost no pressure without the straw. The amount of airflow is much greater without the straw of course.
All the pressure rise is telling you is that there is a resistance to flow but it doesn’t tell you how much flow is taking place. The same thing applies to a turbo engine. What the boost gauge is telling you is how much pressure it takes to generate a given amount of horsepower through the restriction of the head and induction system that the turbo is pushing against. If you reduce the restriction you’ll get more airflow and power at the same boost level or alternatively the same amount of power at a lower boost level.
Heat Management and Intercooling
The Universal Gas Laws tell us that when we compress a gas we also raise its temperature. This is also discussed in the article on doing compression tests. Turbos increase the temperature of the air they compress and this reduces power and increases the engine’s tendency to detonation. This excess heat has to be removed with an intercooler but this adds yet another restriction to flow. The more boost you run the bigger the intercooler needs to be which loses flow again leading to the need for even more boost and eventually you end up in a vicious circle which limits the amount of power the engine can generate.
So the trick is to get more air into the cylinders with as little heat rise as possible. The answer is simple. Reduce the restrictions to flow which then reduces the amount of boost the turbo needs to generate and also the amount of extra heat created. You get more power with less heat and kill two birds with one stone.
Quantifying the Benefits of Cylinder Head Modifications
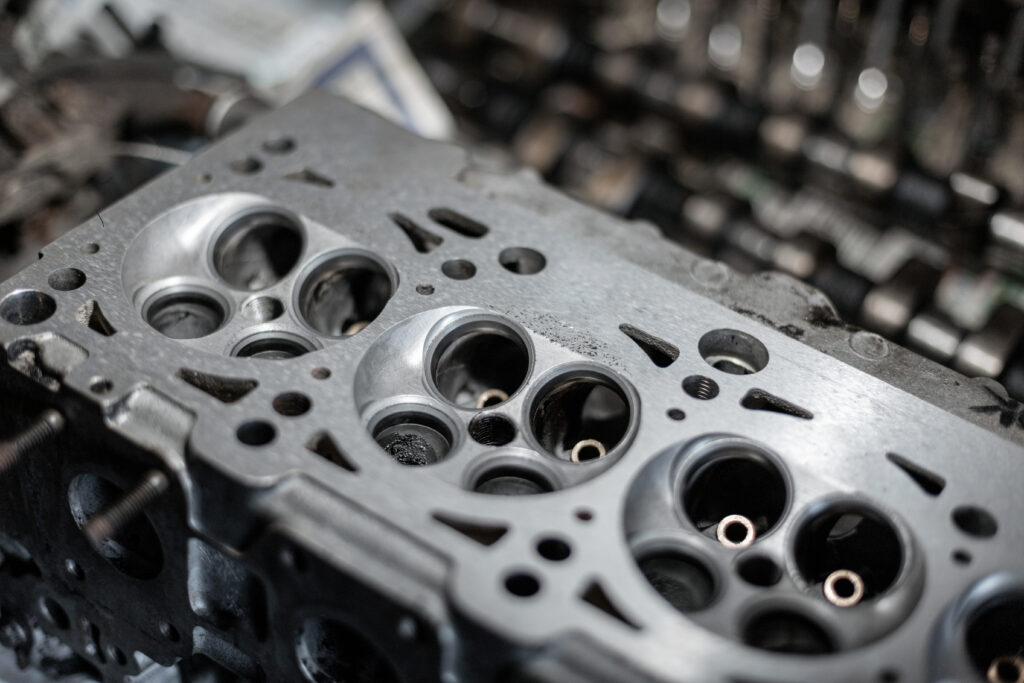
In simple terms if a ported cylinder head gives 20% extra power on a N/A engine it will also give 20% extra power on a turbo’s engine. Maybe even more once the heat drop is taken into account. However, the bhp amount of the power gain will be much higher on the turbo engine because the base power is higher. If you take a 150 bhp N/A engine that extra 20% will add 30 bhp but if the engine is turbocharged to 15 psi boost and produces 300 bhp on the standard head then the 20% extra power from the ported head becomes 60 bhp.
Ported heads and especially big valve ported heads are therefore just as important on turbo charged engines as they are on N/A ones.
Critical Ignition System Considerations
One thing you need to watch out for on turbocharged engines is the spark plug gap. This needs to be smaller than for normally aspirated engines because it takes more voltage to fire a spark across a denser fuel/air mixture. The average 0.8mm to 1mm gap on a N/A engine will need to be reduced to maybe 0.6mm depending on the output of your ignition system or else the engine will give the feeling of running into a brick wall at higher rpm as the boost blows the spark out. If your engine runs ok up to medium rpm and then just stops dead or misfires under boost have a look at this area.
Advanced Turbo Tuning Strategies
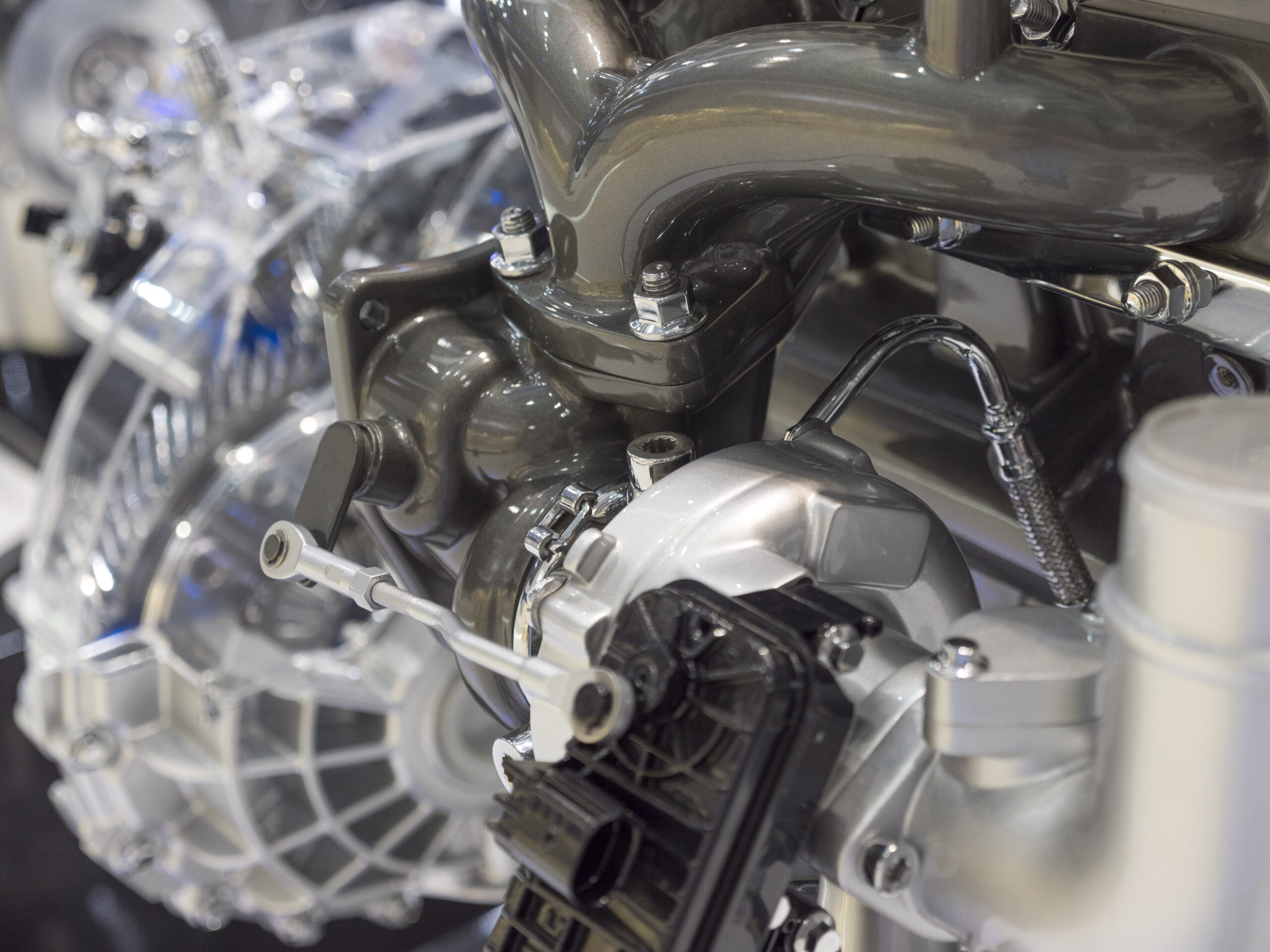
Fuel System Upgrades
When increasing boost pressure and airflow, the fuel system becomes a critical bottleneck. Stock fuel injectors and pumps are typically sized for the engine’s original power output. As boost increases, fuel demand grows exponentially, not linearly. A general rule is that doubling the power output requires roughly 1.8 times the fuel flow capacity due to efficiency losses at higher power levels.
Upgrading fuel injectors should be done with consideration for idle quality and part-throttle drivability. Injectors that are too large can cause poor idle characteristics and fuel economy issues. A staged approach often works best, upgrading injectors in increments as power targets increase.
Exhaust System Optimization
The exhaust side of turbo tuning is often overlooked but equally important. A restrictive exhaust system creates backpressure that the turbo must work against, reducing efficiency and increasing heat. The exhaust manifold, downpipe, and complete exhaust system should be considered as a complete flow path.
Turbo sizing becomes critical here. A turbo that’s too small will create a bottleneck at higher power levels, while one that’s too large will have poor response characteristics at lower RPMs. The concept of “area under the curve” applies – optimizing for peak power often sacrifices mid-range torque and daily drivability.
Engine Management and Tuning
Modern engine management systems allow precise control over fuel delivery, ignition timing, and boost control. Proper tuning requires understanding the relationship between these parameters and how they interact under different operating conditions.
Ignition timing in turbocharged engines requires careful attention to prevent detonation. As boost pressure increases, ignition timing typically needs to be retarded to prevent knock. However, retarding timing too much reduces power and increases exhaust gas temperatures, which can damage the turbo.
Fuel mixture (air-fuel ratio) also requires careful calibration. Rich mixtures provide a cooling effect that helps prevent detonation but reduce power and increase fuel consumption. Lean mixtures increase power but raise combustion temperatures and the risk of engine damage.
Supporting Modifications
Several supporting modifications become necessary as power levels increase. The cooling system must be upgraded to handle increased heat loads. This includes not only the radiator and cooling fans but also oil cooling systems, as turbo engines generate significantly more heat in the engine oil.
The engine’s internals may require strengthening. Connecting rods, pistons, and head gaskets are common failure points in high-boost applications. Forged pistons and rods, along with upgraded head gaskets and head studs, become necessary as power levels increase beyond the engine’s original design parameters.
Boost Control Systems
Proper boost control is essential for both performance and reliability. Simple boost controllers work by bleeding pressure from the turbo’s wastegate actuator, but more sophisticated electronic boost controllers offer features like boost-by-gear, multiple boost maps, and safety limits.
Wastegate sizing and setup significantly affects boost control characteristics. An undersized wastegate will struggle to control boost at higher power levels, while an oversized one may cause boost oscillation or poor boost response.
Common Pitfalls and Troubleshooting
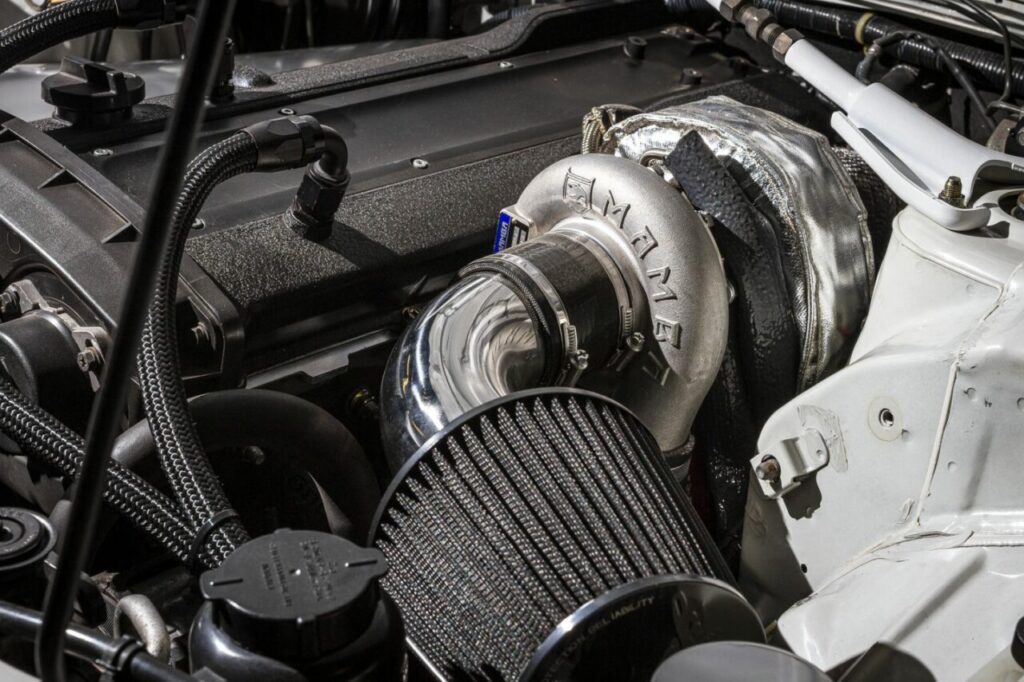
Many turbo tuning projects fail due to overlooking basic principles. Boost leaks are a common issue that can cause poor performance and inconsistent behavior. All connections in the intake system, from the turbo to the throttle body, must be pressure-tested and secured properly.
Heat soak is another common problem, especially in engine bay-mounted intercoolers. As the engine operates, heat from the engine and exhaust system raises the temperature of the intercooler, reducing its effectiveness. Proper intercooler placement and heat shielding can mitigate this issue.
Surge and compressor stall can damage the turbo and create poor drivability. This occurs when the compressor tries to flow more air than the engine can consume, often during rapid throttle closures. Proper blow-off valve sizing and setup prevents these conditions.
Maintenance Considerations
Turbocharged engines require more frequent maintenance than naturally aspirated ones. Oil changes should be performed more frequently due to the extreme operating conditions the oil experiences in the turbo bearing system. High-quality synthetic oils with appropriate viscosity ratings are essential.
Air filter maintenance becomes more critical as any restriction in the intake system directly affects turbo efficiency. Clogged air filters not only reduce power but can cause the turbo to work harder, increasing wear and heat generation.
Regular inspection of the turbo system components, including the wastegate operation, boost control system, and intercooler efficiency, helps prevent small problems from becoming major failures. Monitoring exhaust gas temperatures and keeping detailed logs of performance parameters can help identify developing issues before they cause damage.